CAUTION: For the purpose of the Sustainable Composites pages, the materials
described are those from natural sources, without prejudice to the results of
any future Quantitative Life Cycle Analysis (QLCA) which may (or may not) make
the case for these materials being more environmentally-friendly than equivalent
systems manufactured from man-made fibres and synthetic resins. The inclusion
of any specific system here is not an endorsement of that product: potential
users will need to fully consider each system in the context of their specific
technical requirements.
The value of Eco-System Services
Natural fibres for the reinforcement of polymer
matrix composites are normally the bast fibres (the structural fibres from plant
stems) [1-6]. The principal plants used are flax, hemp, jute and kenaf. There is
growing interest in the potential of nettle fibres. A useful
source for information on a wide variety of plants is the
Crop Index
at Purdue University Center for New Crops and Plant Products - crops are listed
alphabetically by genus and common name. ADAS has recently reviewed and analysed the breeding and regulations of hemp and flax varieties available for growing in the
United Kingdom.
This page considers
The main advantages and disadvantages of natural fibres are listed in Table 1.
Table 1: Main advantages and disadvantages of natural fibres (from Stamboulis et al [7])
ADVANTAGES |
DISADVANTAGES |
Low cost |
High moisture absorption |
Renewable resource |
Poor dimensional stability (swelling) |
Low density |
Poor microbial resistance |
High specific properties |
Low thermal resistance |
High Young's modulus |
Discontinuous fibre |
Good tensile strength |
Anisotropic fibre properties |
Non-abrasive to tooling and moulds |
Low transverse strength |
No skin irritations |
Low compressive strength |
Low energy consumption |
Local and seasonal quality variations |
CO2 neutral |
Demand and supply cycles |
No residues when incinerated |
|
Biodegradable (±) |
|
The main chemical constituents of natural fibres are listed in Table 2 [8]. The fibres themselves can be considered to be a composite with cellulose fibrils in a matrix of hemicelluloses, with lignin accumulating in the matrix as the plant ages [9], and pectin as the cementing/adhesive materials at the interface between the cellulosic and non-cellulosic substances [10]. The thermal degradation of natural fibres occurs in two stages: between 220-280°C mass loss is associated with degradation of the hemicelluloses (~28 kcal/mol), while between 280-300°C the lignin is lost (~35 kcal/mol) [9]. The carbohydrates (cellulose and hemicelluloses) are degraded by biological organisms. The lignicellulosics undergo photochemical degradation due to the ultraviolet frequencies in sunlight [9].
Table 2: The main chemical constituents of natural fibres, with relative abundance of the lignin components
(from S Laurichesse and L Avérous [8]).
Letter | constituent | chemical nature | formula | | |
| cellulose |
β-D-glucopyranose (Fig. 1) | C6H10O5 | | |
| hemicelluloses |
xylans, e.g D-xylopyranose | | | |
|
lignin: monolignol |
basic structures |
hardwood |
softwood |
grasses |
G |
coniferyl alcohol |
guaiacyl |
major |
major |
major |
H |
p-coumaryl alcohol |
p-hydroxyphenyl |
trace |
minor |
minor |
S |
sinapyl alcohol |
siringyl |
major |
- |
major |
| pectins |
complex polyscaccharides with
α-(1,4) linked D-galacturonic acid backbone [10] | | | |
Figure 1: The chemical structure of cellulose (image source)
The properties of natural fibres referenced to those of man-made fibre are shown in Table 3. Šturcová et al [11] measured the modulus of a highly oriented cellulose chain of tunicate cellulose whiskers as 145 GPa. They used a molecular mechanics approach with computer simulation and an empirical force field to predict a modulus of 145 GPa, which was in close agreement with the experimental data.
Table 3: Properties of natural fibres referenced to those
of man-made fibre
(see PowerPoint for comparative bar-graphs of
density,
moduli and
strengths)
|
Density |
Modulus |
Elongation |
Strength |
Diameter |
Reference |
|
kg/m3 |
GPa |
% |
MPa |
μm |
|
Animal |
|
|
|
|
|
|
Silk |
1340 |
10 |
18-20 |
600 |
|
12 |
Grass |
|
|
|
|
|
|
Bagasse |
1250 |
17 |
|
290 |
|
13 |
Miscanthus giganteus |
190-240 |
3.1-3.7 |
- |
23-28 |
- |
14 |
Seed |
|
|
|
|
|
|
Coir |
1150 |
4-6 |
15-40 |
131-175 |
100-450 |
15 |
Cotton |
1520 |
27 |
6-12 |
200-800 |
|
12 |
Leaf |
|
|
|
|
|
|
Abaca (manila hemp) |
1500 [16] |
|
|
980 [16] |
25-40 [17] |
16, 17 |
Sisal |
1450 |
10-22 |
3-7 |
530-640 |
50-300 |
15 |
Pineapple |
1440 |
35-82 |
1.6 |
413-1627 |
20-80 |
15 |
Bast (stem) |
|
|
|
|
|
|
Jute |
1520 |
60 |
2.0 |
860 |
200 [15] |
12 |
Hemp |
1520 |
70 |
1.7 |
920 |
|
12 |
Flax |
1520 |
100 |
1.8 |
840 |
|
12 |
Flax ariane |
1530 |
58 ± 15 |
3.27 ± 0.4 |
1339 ± 486 |
17.8 ± 5.8 |
18 |
Flax agatha |
1530 |
71 ± 25 |
2.1 ± 0.8 |
1381 ± 419 |
15 ± 0.6 |
19 |
Nettle (Urtica dioica) |
|
87 ± 28 |
2.11 ± 0.81 |
1594 ± 640 |
19.9 ± 4.4 |
20 |
Ramie (Boehmeria nivea) |
1500 |
24.5 |
2.5 |
560 |
34 |
21 |
Man-made |
|
|
|
|
|
|
E-glass |
2550 |
71 |
3.4 |
3400 |
|
11a |
S-glass |
2500 |
85 |
4.6 |
4580 |
|
11a |
Aramid (K49) |
1440 |
124 |
2.5 |
2760 |
11.9 |
11a |
High strain carbon |
1820 |
200 |
1.3 |
2550 |
8.2 |
11a |
High modulus carbon |
2020 |
379 |
0.5 |
1720 |
11 |
11a |
However, the cross-section of natural fibres is normally neither circular nor within a tight distribution of apparent diameters. A revised rule-of-mixtures has been proposed to recognise these differences from the case for man-made fibres:

where the two new parameters are:
- κ: the fibre area correction factor (FACF) [22] - set at unity for fibres with a circular cross-sectional area (CSA), with higher vales for natural fibres (Table 4). The FACF accounts for the difference between the true CSA of the irregular cross-section fibre and the apparent CSA based on a "diameter" measured by optical microscopy. Virk et al [23] calculated a FACF of 1.42 for jute being the ratio of the apparent CSA (based on the apparent diameter from transverse microscopy) relative to the true CSA measured from cross-sections, where the CSA had geometric means of 2697 µm2 and 1896 µm2 respectively [23]. The inclusion of the FACF to account for the non-circular cross-section of the natural fibres resulted in improved predictions of both the elastic modulus and the strength of jute fibre composites. Data from other authors was also analysed in order to triangulate these findings for elastic modulus and twelve of the fourteen cases returned an error of significantly reduced magnitude when the above FACF was used.
Table 4: Fibre Area Correction Factors (FACF) for bast (and other) natural fibres sorted by increasing FACF [24. 25].
Fibre |
Apparent diameter (μm) |
FACF |
Source |
Palm (leaf) |
145 | 0.94 | Garat et al [26] |
Flax |
91 | 1.06 | Garat et al [26] |
Sisal (leaf) |
163 | 1.11 | Garat et al [26] |
Flax |
17.3±2.1 | 1.12 | Brierley [27] |
Nettle |
90 | 1.22 | Garat et al [26] |
Curaua (leaf) |
92.3 | 1.27 | Terasaki et al [28] |
Maize |
221 | 1.30 | Connolly [29] |
Jute |
58.6 | 1.297 |
Virk et al [23]: diameter from geometric mean projected width for 50 intervals through 180° |
Jute |
58.6 | 1.303 |
Virk et al [23]: median diameter from projected width for 50 intervals through 180° |
Jute |
58.6 | 1.375±0.485 |
Virk et al [23]: diameter from arithmetic mean projected width for 50 intervals through 180° |
Hemp |
88 | 1.38 | Garat et al [26] |
Flax |
20.4 | 1.39 | Aslan et al [30] |
Jute |
58.6 | 1.42 |
Virk et al [23]: diameter from measurements normal to the Grafil testcard |
Kenaf |
96.8 | 1.47 | Terasaki et al [28] |
Bamboo (grass) |
136.1 | 1.60 | Terasaki et al [28] |
Sisal (leaf) |
162-359 | 1.99 | Thomason et al [31] |
Banana peel |
131 | 2.54 | Ferrante et al [32]: includes lumen |
Flax |
109-218 | 2.55 | Thomason et al [3129] |
Flax |
82±21 | 2.70 | N Soatthiyanon [33, 34] |
Banana peel |
131 | 2.98 | Ferrante et al [32]: excludes lumen |
- and ηd : the fibre diameter distribution factor (FDDF) [35] - set at unity for man-made fibres.
Manufacture of natural fibre reinforced polymer matrix composites
The manufacture of natural fibre reinforced thermoplastic matrix composites is constrained by the degradation temperautre of the fibres being similar to the melting point of many matrix systems. To avoid damage to the fibres, in-situ polymerisation for liquid composite moulding (LCM) processes may be appropriate.
Modelling the manufacture of natural fibre composites is more complex than for the usual synthetic reinforcements due to absorption of the resin system, and consequent swelling of the fibre. This then affects liquid composite moulding processes (e.g. RTM or RIFT) due to changes in the permeability of the reinforcement stack.
Deterioration of natural fibres
Various authors [36-41] have reviewed the fungal deterioration of cellulosic textiles. Montegut et al [40] conclude that water that is physically bound to the fibres appears to be a controlling factor with both bacteria and actinomyceti needing a water activity reading a(w) of at least 0.90 (water has a(w) = 1.0). Few species of fungus can grow below a(w) of 0.8, but severely low relative humidity can lower the a(w) below 0.4 and cause direct damage to the textile.
While humidity and temperature are the strongest influences on colony growth, there are subtle interactions between other factors such as a(w), pH, oxygen and light which determine the overall activity of the microorganisms. The enzymes can continue to degrade fibre after the organism that produced them has been destroyed.
Simoncic et al [41] used an antimicrobial finish based on AgCl in combination with an organic-inorganic reactive binder (RB) and water- and oil-repellent finishes to control biodegradation of
cellulosic (cotton) textiles. AgCl/RB resulted in excellent microbial reduction and hence strong inhibition of biodegradation in soil burial tests.
References
- Caroline Baillie, Green Composites: polymer composites and the environment, Woodhead Publishing Limited, Cambridge, 2004. ISBN 1-85573-739-6. PU CSH Library.
- R R Franck (editor), Bast and other plant fibres, Woodhead Publishing Limited, Cambridge, March 2005. ISBN 1-85573-684-5. PU CSH Library
- AK Mohanty, M Misra and LT Drzal, Natural Fibers, Biopolymers and Biocomposites, CRC Press/Taylor & Francis Group, Boca Raton FL, 2005. ISBN 0-8493-1741-X. PU CSH Library
- Richard Wool and X Susan Sun,
Bio-Based Polymers and Composites, Elsevier, August 2005. ISBN 0-12-763952-7. Overview.
- J Summerscales, N Dissanayake, W Hall and AS Virk, A review of bast fibres and their composites. Part 1: fibres as reinforcements, Composites Part A: Applied Science and Manufacturing, October 2010, 41(10), 1329-1335.
- J Summerscales, N Dissanayake, W Hall and AS Virk, A review of bast fibres and their composites. Part 2:
composites, Composites Part A: Applied Science and Manufacturing, October 2010, 41(10), 1336-1344.
- A Stamboulis, CA Baillie and T Peijs, Effects of environmental conditions on mechanical and physical properties of flax fibers, Composites Part A: Applied Science and Manufacturing, 2001, A32(8), 1105-1115.
- S Laurichesse and L Avérous, Chemical modification of lignins: Towards biobased polymers, Progress in Polymer Science, July 2014, 39(7), 1266–1290.
- DN Saheb and JP Jog, Natural fiber polymer composites: a review, Advances in Polymer Technology, 1999, 18(4), 351-363.
- A Madhu and JN Chakraborty, Developments in application of enzymes for textile processing, Journal of Cleaner Production, 1 March 2017, 145, 114–133.
- A Šturcová, GR Davies and SJ Eichhorn, Elastic modulus and stress-transfer properties of tunicate cellulose whiskers, Biomacromolecules, 15 February 2005, 6(2), 1055–1061.
[11a] NL Hancox, Fibre Composite Hybrid Materials, Elsevier Applied Science, Barking, 1981. ISBN 0-85334-928-2. PU CSH Library
- TJ Reinhart, Engineered Materials Handbook 1: Composites, ASM International, 1987. ISBN 0-87170-279-7. PU CSH Library
- A Balaji, B Karthikeyan and C Sundar Raj, Bagasse fiber - the future biocomposite material: a review, International Journal of ChemTech Research, 2014-2015, 7(01), 223-233.
- Richard Mark Johnson, Innovations and applications in the usage of miscanthus grass: executive summary, Dissertation submitted in partial fulfilment for the degree of Doctorate of Engineering, Warwick Manufacturing Group - School of Engineering - University of Warwick, September 2006 (reproduced here with the permission of Kerry Kirwan).
- N Chand, RK Tiwary and PK Rohatgi, Resource structure properties of natural cellulosic fibres - an annotated bibliography, Journal of Materials Science, 1988, 23(2), 381-387.
- WD Brouwer, Natural Fibre Composites in Structural Components: Alternative Applications for Sisal?, Seminar: Common Fund for Commodities - Alternative Applications for Sisal and Henequen, Food and Agriculture Organization of the UN (FAO) and the Common Fund for Commodities (CFC), Rome, 13 December 2000.
- RM Rowell, AR Sanadi, DF Caulfield and RE Jacobson, Utilization of Natural Fibers in Plastic Composites: Problems and Opportunities,
http://www.fpl.fs.fed.us/documnts/pdf1997/rowel97d.pdf, accessed 22 December 2006 at 12:23.
- C Baley, Analysis of the flax fibres tensile behaviour and analysis of the tensile stiffness increase, Composites Part A: Applied Science and Manufacturing, July 2002, 33(7), 939-948.
- K Charlet, JP Jernot, M Gomina, J Bréard, C Morvan and C Baley, Proceedings of the 12th European Conference on Composite Materials (ECCM-12), Biarritz - France, August/September 2006.
- E Bodros and C Baley, Study of the tensile properties of stinging nettle fibres (Urtica dioica), Materials Letters, 15 May 2008, 62(14), 2143-2145.
- Koichi Goda, MS Sreekala, Alexandre Gomes, Takeshi Kaji, Junji Ohgi, Improvement of plant based natural fibers for toughening green composites - effect of load application during mercerization of ramie fibers, Composites Part A: Applied Science and Manufacturing, December 2006, 37(12), 2213-2220.
- AS Virk, W Hall and J Summerscales, Modulus and strength prediction for natural fibre composites, Materials Science and Technology, 2012, 28(7), 864-871.
- AS Virk, W Hall and J Summerscales, Physical characterisation of jute technical fibres: fibre dimensions, Journal of Natural Fibres, 2010, 7(3), 216-228.
- Summerscales, AS Virk and W Hall, Fibre Area Correction Factors (FACF) for the extendedrules-of-mixtures for natural fibre reinforced composites, Materials Today: Proceedings, 2020, 31(s2), s318-s320. 4th International Conference on Natural Fibers (ICNF2019) ~ smart sustainable solutions.
- J Summerscales, AS Virk and W Hall, Enhanced rules-of-mixture for natural fibre reinforced polymer matrix (NFRP) composites (comment on Lau et al. in volume 136), Composites Part B: Engineering, 1 March 2019, 160, 167-169.
- W Garat, S Corn, N Le Moigne, J Beaugrand and A Bergeret, Analysis of the morphometric variations in natural fibres by automated laser scanning: towards an efficient and reliable assessment of the cross-sectional area, Composites Part A: Applied Science and Manufacturing, May 2018, 108, 114-123.
- MJ Brierley, Fibre area correction factor (FACF) for flax fibre reinforcements, BEng (honours) Mechanical Engineering with Composites project report, University of Plymouth, April 2014.
- Y Terasaki, J Noda and K Goda, Strength evaluation of green composite with variation in cross-sectional area of plant-based natural fibers, Advanced Materials Research, August 2009, 79-82, 235-238 [Special issue on Multi-Functional Materials and Structures II edited by Y Yin and X Wang].
- S Connolly, Agricultural crop residue as a reinforcement in composite material, BEng (honours) Mechanical Engineering with Composites project report, University of Plymouth, May 2019.
- M Aslan, G Chinga-Carrasco, BF Sørensen and B Madsen, Strength variability of single flax fibres, Journal of Materials Science, 2011, 46, 6344–6354.
- JL Thomason, J Carruthers, J Kelly and G Johnson, Fibre cross-section determination and variability in sisal and flax and its effects on fibre performance characterisation, Composites Science and Technology, 04 May 2011, 71(7), 1008–1015.
- A Ferrante, C Santulli and J Summerscales, Evaluation of tensile strength of fibers extracted from banana peels, Journal of Natural Fibers, 2020, 17(10), 1519-1531.
- Niphaphun Soatthiyanon, Separation and characterisation of elementary kenaf fibres as reinforcement in high-density polyethylene-matrix composites and tensile behaviour of flax fibres as reinforcement in vinyl ester-matrix composites, PhD thesis, University of New South Wales, 2014 (restricted until July 2016).
- N Soatthiyanon, A Crosky, and MT Heitzmann, Comparison of experimental and calculated tensile properties of flax fibres, In D Fernando, J-G Teng and JL Torero (editors), Proceedings of the Second International Conference on Performance-based and Life-cycle Structural Engineering (PLSE 2015), Brisbane QLD, Australia, 9-11 December 2015, 116-120.
- J Summerscales, W Hall and AS Virk, A fibre diameter distribution factor (FDDF) for natural fibre composites, Journal of Materials Science, September 2011, 46(17), 5876-5880.
- RGG Siu, Microbial Decomposition of Cellulose, Reinhold Press, New York, 1951.
- JW Howard and FA McCord, Cotton quality study IV: resistance to weathering, Textile Research Journal, February 1960, 30(2), 75-117.
- RS Mahomed, Chapter IX in H Mark, NS Wooding and SM Atlas (editors), Chemical Aftertreatment of Textiles, Wiley-Interscience, New York, 1971.
- TL Vigo,, Protection of textiles from biological attack, in Lewin and Sello, Handbook of Fiber Science and Technology: Volume II: Chemical Processing of Fibers and Fabrics. Functional Finished. Part A, Marcel Dekker, New York, 1983, 367-427.
- D Montegut, N Indictor and RJ Koestler, Fungal deterioration of cellulosic textiles: a review, International Biodeterioration, 1991, 28(1-4), 209-226.
- B Simoncic, B Tomsic, B Orel and I Jerman, Biodegradation of Cellulose Fibers, Nova Science Publishers, 18 Aug 2010. ISBN-13: 978-1-61668-154-8.
Flax (Linum usitatissimum L.) fibres
Flax (grown for fibre) and linseed (grown for seed oil) are cultivars: varieties of the same plant bred with an emphasis on the required product. In the UK the flax plant is normally sown in March-May and may grow to one-metre high dependent on the variety (there are 180 species [F1]). The
Growing Flax page of the Flax Council of Canada (FCC) website [F2] is an especially useful resource giving comprehensive details of the husbandry of this plant:
The life cycle of the plant consists of a 45 to 60 day vegetative period, a 15 to 25 day flowering period and a maturation period of 30 to 40 days and is illustrated in Turner [F3] and the following images from Turner are accessible below via the respective links from the FCC website [F2]. There are 12 distinct growth stages in the flax plant (Table 5):
Table 5: Growth stages and characteristics for flax
Growth Stage |
Characteristics |
1 & 2 |
cotyledon to growing point emerged |
3 & 4 |
1st pair of true leaves unfolded to third pair of true leaves unfolded |
5 |
stem extension |
6, 7, & 8 |
buds visible to full flower |
9, 10 & 11 |
late flower to brown capsule |
12 |
seed ripe |
The typical production cycle for flax fibres [F3] is:
- Drilling (planting) the seed: this usually occurs between the end of February and early April in Belgium, France and the Netherlands or in early April in Northern Ireland (NI). For flax in NI, the suggested levels of fertiliser are 20 kg N/ha, 20 kg P2O5/ha and 80 kg K2O/ha.
- Weed control: it is essential to minimise weeds to avoid contamination of the scutched flax fibres.
- Plant growth: as described in the previous paragraph.
- Dessication: glyphosate is typically applied 10-14 days after full flower, at about mid-July in NI.
- Harvest: by either combining or pulling, in August/September.
- Rippling: the removal of flax seed capsules by drawing pulled stems through a coarse steel comb.
- Retting is defined for flax as the “subjection of crop or deseeded straw to chemical or biological treatment to make the fibre bundles more easily separable from the woody part of the stem. Flax is described as water-retted, dew-retted or chemically–retted, etc., according to the process employed” [Textile Institute,1975]. Enzymes (e.g. pectinase digests pectin binder) may be used to assist the retting process, but termination of the retting process may be a problem and failure to achieve this can result in reduced fibre properties. Pre-harvest retting of flax with glyphosate [F4] applied at the mid-point of flowering depends on uniform desiccation of the entire stem and is difficult to achieve during a dry season. As in dew-retting, stand-retting of the desiccated flax in the field relies on microorganisms and is dependent on the vagaries of the weather. Shekhar Sharma et al [F4] have presented and discussed the role of microbial enzymes, screening of flax cultivars, fibre quality and upgrading of coarse fibres in this context.
Bezazi et al [F5] have reported the development of two innovative extraction methods for the separation of fibres from Agave americana leaves. Both techniques are claimed to be "sustainable" as they do not involve chemical treatments . In the first method, the leaves were buried under 300-400 mm of soil for three months. In the second method, the leaves were immersed [in water] in a barrel for a period of 10–13 days: the closed barrel accelerates the biodegradation process due to the rapid development of the bacteria in a closed environment while reducing water vapourisation. The fibres from the first method had low water demand and "exhibited in general higher tensile modulus and strength compared to water-extracted fibres".
- Degumming is a term used in the context of bast fibres for textile applications (but is rare in the context of reinforcement fibres). Liu et al [F6] state that the fibre is extracted by degumming the plant stem using biological, chemical, or biochemical methods but also that existing degumming methods (whether biological, chemical, or biochemical) have their limits in refining fibre as they make the fibre finer and softer at the cost of reducing fibre tenacity and length (both of the latter parameters would be detrimental to the effectiveness of a reinforcement). Bing and Laijiu [F7] state in comparison to fibre obtained by conventional chemical degumming process, those degummed by bio-enzymatic process possess smoother surfaces, better softness, high strength, excellent spinning ability, and could produce high quality fibre for textile industry. However, they also state that systematic research concerning the bio-degumming mechanism at the molecule scale is not yet found in the literature”
- Decortication is the mechanical removal of non-fibrous material from retted stalks or from ribbons or strips of stem or leaf fibres to extract the bast fibres. For flax, the process is usually referred to as “scutching”. This is usually achieved by a manual operation, hammer mill, inclined plane/fluted rollers, steam explosion or willower. Harwood et al [8] have described a novel environmentally-friendly and cost-effective method using shock waves generated by high-voltage pulsed electrical discharges (HVPED) on fibres immersed in water. The Ultrafibre consortium based at Smithers Rapra is developing a "radial cell process for the clean, continuous, high volume production by hydro-acoustic decortication of high quality natural fibres for the SME natural fibre sector".
- Hackling is the combing the line flax in order to remove short fibres, parallelise the remaining long (line) fibres and also remove any extraneous matter (shive).
- Carding is defined as “the disentanglement of fibres by working them between two closely spaced, relatively moving surfaces clothed with pointed wire, pins, spikes or saw teeth” [9]. The product of this process is known as sliver.
Woollen yarn, prepared by carding, has a fuzzy appearance when woven or knitted. Worsted yarn, prepared by combing, has a smooth appearance as preferred for woven cloth but at the expense of greater waste fibre.
- Spinning is the "drafting [decreasing the mass per unit length] and twisting of
natural (or man-made) fibres". The product of this process is known as yarn or filaments. In the bast- and leaf-fibre industries, the terms ‘wet spinning’ and ‘dry spinning’ refer to the spinning of fibres in the wet state, and in the dry state respectively”. Li Yan [10] has reported evidence of fibre damage (i.e. transverse crushing and collapsed lumen) consequent upon spinning natural fibres into a yarn. Further, voids within composites manufactured from the spun tows were found to increase with the number of turns per metre (tpm).
- Reportage LIN tous débouchés au Teillage Van Robaeys - Killem (Nord Pas de Calais, France) (12' 51" video of flax processing with French sountrack)
A similar route is followed for the other bast fibres. Subsequent treatments may be applied to natural fibre textiles to promote physical and/or chemical adhesion to the matrix for composites. Similar enhancements may be achieved by modification of the matrix, e.g. poly(propylene-co-maleic anhydride) instead of PP, or by the inclusion of compatibilising agents in the matrix to bridge the properties of the hydrophilic fibre and the hydrophobic matrix.
The hierarchy of flax fibres from nano- to micro-scale is shown in Figure 2 with typical dimensions indicated in Table 6.
Figure 2: The hierarchy of flax fibres. Fibre bundles, known as technical fibres, are produced by mechanical decortication (breaking, scutching and hackling) and are ~1 m long and consist of ~10–40 elementary fibres, known as single fibres.
The elementary fibres have lengths of between 20-50 mm and diameters between 5-35 μm. (reproduced from Harriëtte Bos, Jörg Müssig and Martien JA van den Oever
in Composites Part A).
Table 6: Dimensions of the elements of plant fibres [11]
Element |
"Diameter" (nm) |
Cellulose microfibril |
2-4 nm |
Cellulose mesofibril |
200 nm |
Cellulose macrofibril |
100-200 nm |
P |
200-500 nm |
S1 |
500-2000 nm |
S2 |
5000-10000 nm |
S3 |
500-1000 nm |
P+S1+S2+S3 |
6200-13500 nm |
The elementary fibre is normally considered to be a series of contiguous concentric tubes [F12, F13]:
- (centre) lumen: the luminal cavity may be open channel or pectic materials (up to 25% of total CSA),
- secondary (S3): provides cell stability by resisting hydrostatic pressure,
- secondary (S2): the mail bulk of the seconrdary layer has low microfibrillar angle to provide axial stiffness and strength (up to 90% of total cell wall thickness),
- secondary (S1): control fibre stability in compression,
- primary (P): less than 2% of total cell wall thickness.
- (outside) middle lamella (M): glues adjacent cells together.
At the end of life, there is potential for controlled degradation of cellulose fibres by composting or other methods.
Kvavadze et al [F14-F15] found bast fibres in clay in the Dzudzuana cave in Georgia. The specific layer where 488 fibres were found was 14C radiocarbon dated to 32,000-26,000 years (before present). Kvavadze et al used optical and electron microscopy to charactetise the fibres as flax, but Bergfjord et al [F16] suggested they could be a different bast fibre given that only flax or cotton were used as comparators. Kvadadze [F17] responded that specific traits associated with flax were evident in the analysed fibres.
Li et al [F18] found evidence of the emergence of fibrecraft specialisation in early Neolithic period at Peiligang in North China around 8000 years ago. Eurasian vegetable fibre textile fragments date back to the Bronze Age (seventh/sixth millennium BCE) [F19-F23].
In 1941, flax fibres (and hemp) were used in resin matrix composites for the bodywork of a Henry Ford car [F1]. Flax is amongst the natural fibres now finding use in thermoplastic matrix composite panels for internal structures (door panels, parcel shelves and boot linings) in the car industry.
References (F-series)
- Anna Lewington, Plants for People, Eden Project Books/Transworld Publisher, London, 2003. ISBN 1-903-91908-8. PU CSH Library.
- Flax Council of Canada
- John Anthony Turner “Linseed Law: A handbook for growers and advisers”, BASF (UK) Limited, Hadleigh - Suffolk, June 1987. ISBN 0-9502752-2-0. PU CSH Library.
- HSS Sharma, PC Mercer and AE Brown, Review of recent research on the retting of flax in Northern Ireland, International Biodeterioration, 1989, 25(5), 327-342.
- A Bezazi, A Belaadi, M Bourchak, F Scarpa and K Boba, Novel extraction techniques, chemical and mechanical characterisation of Agave americana L. natural fibres, Composites Part B: Engineering, November 2014, 66, 194-203.
- Lifang Liu, Qianli Wang, Zhaopeng Xia, Jianyong Yu and Longdi Cheng, Mechanical modification of degummed jute fibre for high value textile end uses, Industrial Crops and Products, January 2010, 31(1), 43-47.
- Du Bing and Zheng Laijiu, Bio-degumming process on jute fiber for textile, Journal of Biotechnology, October 2008, 136 supplement, S474.
- R Harwood, V Nusenbaum and J Harwood, Cottonisation of flax, International Conference on Flax and Other Bast Plants (Fiber Foundations - Transportation, Clothing and Shelter in the Bioeconomy), Saskatoon (Saskatchewan), CANADA, 21-23 July 2008, Paper ID #22, pages 118-128. ISBN 978-0-9809664-0-4.
- CA Farnfield and PJ Alvey, Textile Terms and Definitions - seventh edition, The Textile Institute, Manchester, 1975. ISBN 0-900739-17-7.
- L Yan, Potentials of plant fibre reinforced composites in views of mechanical and physical performances, First International Conference on Advanced Composites in Marine Engineering (ICACME 2013), Beijing, 11 September 2013.
- C Baley, A Le Duigou, A Bourmaud, P Davies, M Nardin and C Morvan, Reinforcement of polymers by flax fibers: role of interfaces, Chapter 6 in W Smitthipong, R Chollakup and M Nardin (editors), Bio-Based Composites For High-Performance Materials: from strategy to industrial application, CRC Press, Boca Raton FL, 2015, pp 87-112. ISBN 978-1-4822-1448-2.
- DU Shah, Developing plant fibre composites for structural applications by optimising composite parameters: a critical review, Journal of Materials Science, September 2013, 48(18), 6083-6107.
- M George, M Chae and DC Bressler, Composite materials with bast fibres: structural, technical, and environmental properties, Progress in Materials Science, October 2016, 83, 1-23.
- (a) E Kvavadze, O Bar-Yosef, A Belfer-Cohen, E Boaretto, N Jakeli, Z Matskevich and T Meshveliani, 30,000 years old wild flax fibers - testimony for fabricating prehistoric linen, Science, 11 September 2009, 325(5946), 1359-1361.
- Corrections and Clarifications, Science, 16 October 2009, 326(5951), 366.
- C Bergfjord, S Karg, A Rast-Eicher, M-L Nosch, U Mannering, RG Allaby, BM Murphy, B Holst, Comment on “30,000-Year-Old Wild Flax Fibers”, Science, 25 June 2010, 328(5986), 1634.
- E Kvavadze, O Bar-Yosef, A Belfer-Cohen, E Boaretto, N Jakeli, Z Matskevich and T Meshveliani, Response to Comment on “30,000-Year-Old Wild Flax Fibers”, Science, 25 June 2010, 328(5986), 1634.
- L Liu, Y Li, R Chen, Y Cui, X Chen and W Gu, Emergence of fibrecraft specialization 8000 years ago in early Neolithic North China, The Holocene, OnlineFirst 31 July 2024.
- EJW Barber, Prehistoric Textiles: the development of cloth in the Neolithic and Bronze Ages with special reference to the Aegean, Princeton, 1992, 10–12. ISBN 978-0-6910-0224-8.
- L Bender Jørgensen, North European Textiles until AD 1000, Aarhus University Press, Aarhus, 1992, 116. ISBN 978-87-7288-416-5
- M Rottoli, Il lino, in M Bazzanella, A Mayr, L Moser and A Rast-Eicher (editors): Textiles: intrecci e tessuti dalla preistoria europea, Museo Civico di Riva del Garda-La Rocca, Trento, 2003, 65–72. ISBN 88-86602-65-0.
- C Breniquet and C Michel (editors): Wool Economy in the Ancient Near East and the Aegean: from the beginnings of sheep husbandry to institutional textile industry (Ancient Textiles Series 17), Oxbow Books, Oxford, 2014. ISBN 978-1-7892-5380-1.
- S Sabatini and S Bergerbrant (editors), Textile Production and Specialisation in Bronze Age Europe: production, specialisation, consumption, Cambridge University Press, Cambridge UK, 20 November 2019. ISBN 978-1-10865640-5
Background material includes:
- Alister D Muir and Neil D Westcott, Flax: The genus Linum, CRC Press, Boca Raton FL, 2003. ISBN 0-4153-0807-0. PU CSH Library.
- J Salmon-Minotte and RR Franck, Chapter 3: Flax, In RR Franck, Bast and other Plant Fibres, Woodhead Publishing, Cambridge, 2005. ISBN 1-85573-684-5. PU CSH Library
- HS Shekhar Sharma and CF van Sumere, The biology and processing of flax, M Publications, Belfast, c1992. ISBN 0-9519963-0-4. PU CSH Library
- Flax (Linen)
- Interactive European Network for Industrial Crops and their Applications: flax and linseed.
For review papers on flax fibres follow the link.
Published papers on natural fibres ~ flax
Hemp (Cannabis sativa L.) fibres
Hemp is an annual plant native to central Asia and known to have been grown in China over 4500 years ago [H1]. It probably reached central Europe in the Iron Age (circa 400 BC) and there is evidence of growth in the UK by the Anglo-Saxons (800-1000 AD). It does not require fertiliser, herbicides or pesticides to grow well (and hence is potentially of great interest in the context of sustainability). In suitable warm conditions, it can grow to 4 metres in just 12 weeks.
In 1941, hemp fibres (and flax) were used in resin matrix composites for the bodywork of a Henry Ford car which was able to withstand ten-times the impact on an equivalent metal panel [H1]. Hemp is amongst the natural fibres now finding use in thermoplastic matrix composites for internal structures (door panels, parcel shelves and boot linings) in the car industry.
H1. Anna Lewington, Plants for People, Eden Project Books/Transworld Publisher, London, 2003. ISBN 1-903-91908-8.
Background material includes:
- Hemp fibre (East Yorkshire Hemp Company)
- Jersey Hemp (Channel Islands)
- Physical, Chemical and Pulping Characteristics of Hemp
- Michael Karus: European hemp industry 2001: cultivation, processing, and product lines
- Marianne Leupin: New processing with hemp
- Bo Madsen: Properties of Plant Fibre Yarn Polymer Composites - An Experimental Study, PhD thesis, Technical University of Denmark, Report BYG·DTU R-082, 2004. ISSN 1601-2917. ISBN 87-7877-145-5
- J Sponner, L Toth, S Cziger and RR Franck, Chapter 4: Hemp, In RR Franck, Bast and other Plant Fibres, Woodhead Publishing, Cambridge, 2005. ISBN 1-85573-684-5. PU CSH Library
|
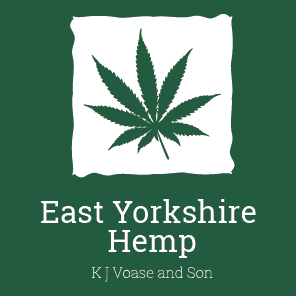 |
 |
Jute (Corchorus capsularis. L. - white jute or C. olitorius L. - Tossa jute) fibres
Jute is the second most common natural fibre (after cotton) cultivated in the world. It is an annual plant that flourishes in monsoon climates and grows to 2.5-4.5 m [J1]. It is primarily grown in Bangladesh, Brazil, China, India and Indonesia. Jute-based thermoplastic matrix composites find a substantial market in the German automotive door-panel industry (growing from 4000 tons in 1996 to over 21000 tons in 1999 and rising) [J1].
Ray et al [J2] determined that the NINFET-Sathi retting formulation [J3] used as a micobial food supplement could halve the time for jute retting to 10-12 days. Fibre yields were increased by 8-11% and fibre quality was improved by up to 1.5 grade.
J1. Anna Lewington, Plants for People, Eden Project Books/Transworld Publisher, London, 2003. ISBN 1-903-91908-8.
J2. DP Ray, RK Ghosh, B Saha, A Sarkar, A Singha, N Mridha, I Das, G Sardar, J Mondal, Manjunatha and BSDB Shakyawar, Accelerated retting technology for the extraction of golden fibre from the Indian Tossa jute (Corchorus sp.), Journal of Cleaner Production, 20 December 2022, 380(2), 135063.
J3. DP Ray, RK Ghosh, B Saha and A Sarkar, Retting accelerator composition for retting of whole jute plant and mesta plants and the process of retting involving the same, Indian Patent Application 201931020813, 2019.
Background material includes:
For review papers on jute fibres follow the link.
Hibiscus (kenaf: H. cannabinus L. and roselle (H.sabdariffa L.) fibres
Kenaf is a fibre plant native to east-central Africa, and a common wild plant of tropical and subtropical Africa and Asia. It has been grown for several thousand years for food and fibre. The plant has a unique combination of long bast with short core fibres in place of the hollow core. Strong interest is being shown in this plant in Malaysia as it is fast growing and hence can yield two crops/year in the local climate.
Roselle bast fibres have potential as the reinforcement for composites (see the review papers link below).
Background material includes:
- T Nishino, Chapter 4: Natural fibre sources, in C Baillie, Green Composites: Polymer Composites and the Environment, Woodhead Publishing, Cambridge, 2004, pp 49-80. ISBN 1-85573-739-6. PU CSH Library.
- PJ LeMahieu, ES Oplinger and DH Putnam: Alternative Field Crops Manual: Kenaf, April 1991.
- Charles S Taylor: Kenaf: an emerging new crop industry, 1993 (in New Crops, 1993).
- Daniel E Kugler: Kenaf commercialisation: 1986-1995 (in Progress in New Crops, 1996).
- T Sellers, GD Miller, MJ Fuller, JG Broder and RR Loper: Lignocellulosic-Based Composites Made of Core From Kenaf, An Annual Agricultural Crop, XX World Congress, International Union of Forest Research Organisations, Tampere - Finland, 06-12 August 1995, S5.05-01 Wood-Based Composites; Improving Our Understanding of Processes and Products.
For review papers on kenaf fibres follow the link.
For review papers on roselle fibres follow the link.
Published papers on natural fibres ~ kenaf
Nettle (Urtica dioica) fibres [N1]
Nettles yield ~ 8-10 tonnes fibre/acre [N2] and are far stronger than cotton but finer than other bast fibres such as hemp. They are a much more environmentally friendly fibre crop than cotton, which requires more irrigation and agrochemical input.
Merilä [N3] has reported elastic moduli and strengths for nettle fibre composites as in Table 7:
Table 7: Characteristics of nettle fibre composites [N3]
Composite |
Modulus |
Strength |
24 v/o nettle/epoxy |
9 GPa |
91 MPa |
23 v/o nettle/phenolic |
5 GPa |
13 MPa |
whereas 21 v/o flax/epoxy was reported to have “strength and stiffness are
more than twice as high”.
Lewington [N4] states that "during the Second World War ... Britain's Ministry of Aircraft Production experimented with the use of a very strong, high-grade paper made from nettle fibre for reinforcing plastic aircraft panels as well as gear wheels and other machine parts".
N1. J Harwood and G Edom, Nettle fibre: its prospects, uses and problems in historical perspective, Textile History, 2012, 43(1), 107-119.
N2.
http://jacksonsrow.topcities.com/tikun_olam/nettle.html
N3. Ann-Jeanette Merilä,
Stinging nettle fibres as reinforcement in thermoset matrices, MSc Engineering/Materials Technology, Luleå University of Technology, 2000.
N4. Anna Lewington, Plants for People, Eden Project Books/Transworld Publisher, London, 2003. ISBN 1-903-91908-8. PU CSH Library.
N5. J Dreyer and G Edom, Chapter 9.5: Nettle, In RR Franck, Bast and other Plant
Fibres, Woodhead Publishing, Cambridge, 2005. ISBN 1-85573-684-5. PU CSH Library
N6. IGP Agus Suryawan, NPG Suardana, IN Suprapta Winaya, IW Budiarsa Suyasa and TG Tirta Nindhia [27 references], Study of stinging nettle (urtica dioica L.) fibers reinforced green composite materials: a review, 2017 IOP Conference Series: Materials Science and Engineering, 2017, 201, 012001, 1-7. 7th International Conference on Key Engineering Materials (ICKEM 2017), Penang - Malaysia, 11-13 March 2017.
For review papers on nettle fibres follow the link.
Other potential natural reinforcement fibres
Animal fibres:
Shah et al asked whether silk might become an effective reinforcing fibre, and made property comparisons between silk, flax and glass reinforced composites [A1].
Bamboo fibre:
BEWARE of fibres marketed as "bamboo". Whilst some naturally retted bamboo fibre is commercially available (albeit scarce), the significant majority should be labelled as "bamboo viscose" as it is chemically processed to solution (similar to Lyocel, Modal®, Tencel® made from wood) before re-spinning into regenerated cellulosic fibre. The processing can significantly compromise any "green" claims for the regenerated fibre [B1].
Cereal crops:
Mamun et al have consdered the use of maize, oat, barley and rye fibres as reinforcements in composites [C1].
References
A1. DU Shah, D Porter and F Vollrath, Can silk become an effective reinforcing fibre? A property comparison with flax and glass reinforced composites, Composites Science and Technology, 12 September 2014, 101, 173-183.
B1. Anon., Bamboo and the FTC, https://oecotextiles.wordpress.com/category/fibers/bamboo/ accessed on 04 November 2014.
C1: AA Mamun, HP Heim and AKBledzki, The use of maize, oat, barley and rye fibres as reinforcements in composites Chapter 15 in Biofiber Reinforcements in Composite Materials, 2015, 454-487.
Further reading
- RR Franck, Bast and other plant fibres, Woodhead Publishing, Cambridge, March 2005. ISBN 1-85573-684-5. PU CSH Library
- AK Mohanty, M Misra and LT Drzal,
Natural fibers,
biopolymers, and biocomposites, Taylor and Francis, Boca Raton FL, 2005.
ISBN 978-0-8493-1741-5. PU CSH Library
- AD Muir and ND Westcott,
Flax: the
genus linum, CRC Press, London, 2003. ISBN: 978-0-415-30807-6. PU CSH Library.
- K Pickering, Properties and performance of natural-fibre composites, Woodhead Publishing, Cambridge, 2008. ISBN-13: 978 1 84569 267 4.
- HSS Sharma and CF van Sumere - The biology and processing of flax, M
Publications, Belfast, 1992. ISBN 0-951996-30-4. PU CSH Library
- JA Turner, Linseed law: a handbook for growers and advisers, BASF, Hadleigh, 1987. ISBN 0-950275-22-0. PU CSH Library.
- FT Wallenberger and N Weston,
Natural fibers, plastics and composites, Springer, 2004, ISBN
978-1-4020-7643-5.
- SV Joshi, LT Drzal, AK Mohanty and S Arora -
Are natural
fiber composites environmentally superior to glass fiber reinforced
composites?, Composites Part A: Applied Science and Manufacturing, 2004,
35(3), 371-376.
- A Stamboulis, CA Baillie and T Peijs,
Effects of
environmental conditions on mechanical and physical properties of flax fibers,
Composites Part A: Applied Science and Manufacturing, August 2001, 32(8),
1105-1115.
- Peter Zugenmaier -
Conformation and
packing of various crystalline cellulose fibers, Progress in Polymer
Science, 2001, 26(9), 1341-1417.
- Yan Li, Yiu-Wing Mai and Lin Ye -
Sisal fibre and its
composites: a review of recent developments, Composites Science and
Technology, 2000, 60(11), 2037-2055.
- J Schurz, A bright
future for cellulose, Progress in Polymer Science, 1999, 24(4), 481-483.
- AK Bledzki and J Gassan,
Composites
reinforced with cellulose based fibers, Progress in Polymer Science, 1999,
24(2), 221-274.
- HSS Sharma, PC Mercer and AE Brown,
A review of recent
research on the retting of flax in Northern Ireland, International
Biodeterioration, 1989, 25(5), 327-342.
- J Summerscales, N Dissanayake, W Hall and AS Virk, A review of bast fibres and their composites. Part 1: fibres
as reinforcements, Composites Part A: Applied Science and Manufacturing, October 2010, 41(10), 1329-1335.
- J Summerscales, N Dissanayake, W Hall and AS Virk,
A review of bast fibres and their composites. Part 2: composites, Composites Part A: Applied Science and Manufacturing, October 2010, 41(10), 1336-1344.
- J Summerscales, AS Virk and W Hall, A review of bast fibres and their composites. Part 3: modelling, Composites Part A: Applied Science and Manufacturing, 2013, 44(1), 132-139.
- J Summerscales, Virtual book on bast fibres and their composites.
Other resources
Return to MATS 347 home page
Updated by John Summerscales on
07-Aug-2024 13:31. Terms and conditions. Errors and omissions. Corrections.